8 Typical Mixing Errors and How to Prevent Them
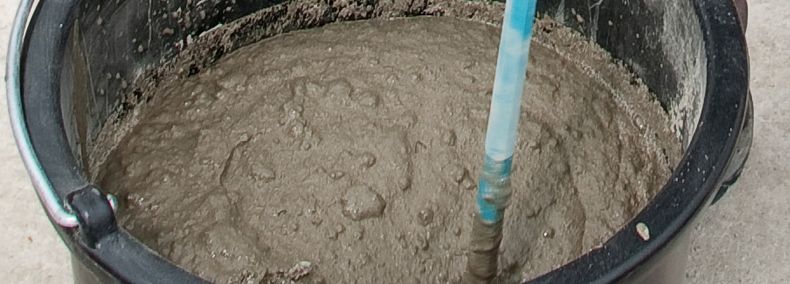
Mixing jobs are a big part of the daily work on construction sites and improperly mixed concrete can create unacceptable or substandard results. This often leads to construction damages and/or additional costs. It’s the right mixture that matters. The question is: How can you avoid these mixing errors?
Mixing Error No. 1: Using the wrong mixing paddle or use
Are you using only one mixing paddle for every mixing material? Different building materials have different mixing requirements. By using the wrong mixing paddle your material is not properly homogenized. It often creates strong lump formations in your mixture. For example: self-leveling compounds need a very special mixing paddle with high shear forces, like the Collomix KR series. Using an ordinary mortar mixing paddle with self-leveling compounds will exceed the paddles mixing limit.
Mixing Error No. 2: Too large or too small mixing bucket
The right size bucket can also hinder mixing results. When choosing a mixing bucket you should take into consideration the entire mixing quantity. If you select too small of a mixing bucket, the material may splash out of the bucket during mixing. This will unnecessarily pollute your working environment and it also leads to unnecessary material loss. To recognize the right mixing bucket size, make sure the basket of the mixing paddle is completely covered by the mixing material in the bucket.
Mixing Error No. 3: Wrong mixing technology – Unsuitable mixing tools
Many building materials need a specialized mixing technology and/or a specialized mixing tool. Before mixing you need to consider the specifications of your material. For example, if you mix two component reaction resin mortars with nothing but a standard power drill and a standard mixing paddle, you can possibly cause considerable construction damages. When mixing 2 component materials, the right mixing technology must be chosen with great care. Otherwise, problems like sticky spots may occur after the material has hardened. Therefore, it is recommended to pre-mix both components (resin & hardener) in separate mixing buckets, before the final homogenization of both materials. And if adding quartz sand into the mixture, you should consider using a special compulsory mixer.
Mixing Error No. 4: Wrong mixing action
The correct mixing action is very important for perfect results. Before you begin mixing, you’ll need to consider if the material will be mixed from bottom to top or if you’ll be mixing from the top to the bottom. Mixing incorrectly not only makes your mixing jobs much more difficult, it also can also ruin your mixed materials.
For example, when you mix screed or mortar with the wrong mixing action, you can cause material residues on the bottom of your mixing bucket. By using an incorrect paddle and mixing action, your mixing jobs become much more difficult or the material will not be suitable for the job.
Mixing Error No. 5: Too short mixing times / incomplete mixing results
Mixing under time pressure isn’t a good idea. Errors during mixing may compromise the performance of your product. If a too short mixing time is selected or mix intensity is insufficient the dispersion of all components cannot be guaranteed. The consequence: Time-consuming repair work e.g. lack of adhesion, cavities or pop-outs, etc.
Mixing Error No. 6: Heavily soiled mixing paddles
And now hand on heart. How often are you cleaning your mixing paddle? Directly after every mixing job? If your answer is no, then you should do this much more often in the future. Dried material residues may come off and contaminate your new material with foreign particles. Even worse, several material layers can make your mixing paddle useless. In addition, extremely dirty mixing paddles must be replaced much more often, which can quickly become expensive. Our special cleaning bucket Mixer-Clean will help you to clean your mixing paddles quick and easy.
Mixing Error No. 7: Mixer with insufficient speed
It is very important to choose the correct speed when mixing. If the speed of your mixer is too weak, the components of your mixing material (Liquid & Powder) will not be mixed together. For example, the spread properties of self-leveling-compounds will very quickly become substandard. Consequently, more work and a higher material requirement will be necessary, not to mention unnecessary working hours and additional mixing material costs your money and frayed nerves.
Mixing Error No. 8: Ignore the specified sequence of the mixing instructions
Do you always follow the mixing instructions of the material manufacturer? First add water, then mixing material, or vice versa? Or do you not care about the instructions? Unfortunately this practice may cause problems like strong lump formations or a complicated processing. The consequence of this is a high need for expensive reworking. Sometimes the mixture will become useless and must be discarded – which also cost unnecessary money.
Recognize mixing errors – Prevent mixing errors: Saves your time and money on every site.