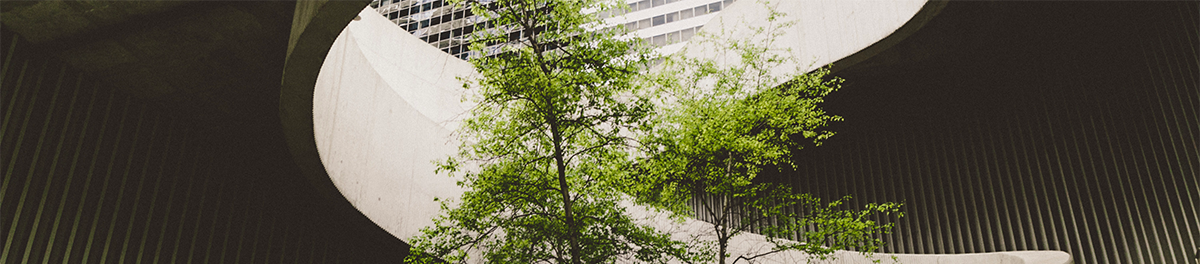
Seven Concrete Sustainability Technologies You Should Already Be Using
In 2015, alongside 195 other countries, Australia agreed on the United Nations Paris agreement on climate change. This agreement is to limit emissions globally by 2050, known as the Net Zero initiative. Working together towards reducing the amount of carbon dioxide emitted into the atmosphere.
Currently, 40% of energy related greenhouse gas emissions are generated from the building and construction sector. With up to 8% of this coming from concrete production and another 8% from steel, closely followed by aluminium and then other construction materials. This agreement, plus the continued general environmental concern see’s the Australian construction market stakeholders shifting to and insisting on sustainable construction solutions. As Australia moves towards a more sustainable approach in aims to reach its targets, the construction industry is being asked “Are all we are putting our best possible foot forward?”
“The raw materials are virtually limitless, and it (concrete) will be in demand for as long as we build roads, bridges and anything else that needs a foundation”.
– Phil Purnell, Professor of Materials and Structures, University of Leeds.
Second only to water, concrete is one of the most widely consumed materials on the planet and is the cornerstone of the construction materials industry. The production of cement has increased more than thirtyfold since 1950, and almost quadrupled since 1990. Despite the undeniable environmental impact of cement production; given its durability, long lifespan, versatility and thermal insulation properties, concrete will continue to be the foundation for construction for decades to come.
Darren Steinberg, Chief of industry leading real estate and building company DEXUS, urges that “the world is moving very quickly. If the industry and sector does not get behind some of this technology, it is going to be laggard in its performance” when discussing ‘CarbonCure’, an innovative sustainability technology which works to inject recycled carbon dioxide into fresh concrete, making the concrete stronger and enabling mix optimisation which in turn reduces the concrete’s carbon footprint.
Here’s the good news: Within the Australia building and construction industry we have a number of sustainable concrete solutions ready to go today. Even better, many of these are not only cost neutral to switch to, but can also provide faster, smarter and safer building practices.
Let’s have a look at the top seven sustainable concrete solutions at CE that you should be using today.
CarbonCure
CarbonCure
1. CarbonCure
CarbonCure Technologies is a Canadian Cleantech company that develops carbon dioxide removal (CDR) solutions for the concrete industry. In 2020 CE Construction Solutions became one of CarbonCure’s first Authorised Distributors and began delivering this innovative construction solution to the Australian market.
CarbonCure injects a precise dosage of carbon dioxide (CO2) into concrete during the batching process. When injected into the wet concrete, the CO2 reacts with the calcium ions from cement to chemically convert into a nano-sized mineral, Calcium Carbonate (CaCo3). The CaCo3 disperses through the mix matrix making the concrete stronger, enabling mix optimisation while embodying and eliminating Co2.
Specifying and using CarbonCure as part of your concrete supply is likely to be a cost neutral change with a huge sustainability upside and improved overall concrete performance.
Want to know more about this exciting innovation in sustainable concrete? Click here.
2. E-Mesh
An Australian innovation, Emesh by Fibercon utilises 100% recycled plastic to deliver an innovative, sustainable, greener reinforced concrete for pavements and footpaths.
These Australian manufactured recycled plastic macro polypropylene fibres are added to concrete to replace shrinkage steel. Emesh completely replaces non-recycled plastic fibres or steel reinforcing mesh. According to a James Cook University Study, this technology reduces carbon emissions and fossil fuel usage by 90% when compared to traditional steel mesh reinforcing. As of May 2018, Emesh has replaced over 330 tons of steel mesh reducing CO2 by 1000tons and reused over 50 tons of waste plastic. This is equivalent to taking 214 cars off the road for 1 year.
“If we replaced all the steel mesh in footpaths and light pavement with Emesh, we would reduce our CO2 by 125,000 tons annually, and re-use 5000 tons of waste plastic”, said Mark Combe, Founder of Fibercon “It’s an exciting goal for us.”
Specifying and using Emesh as part of your concrete supply package is likely to reduce cost, enable faster and simpler concrete placement, provide a safer working environment during install, reduce future maintenance cost on the infrastructure it’s applied and provide a huge sustainability upside.
Interested in understanding more about the impact Emesh could have in your next project? Speak with us today.
3. Cupolex
The Cupolex foundation system is an environmentally friendly alternative to waffle-pods and traditional raft slab foundations. This light weight dome formwork system can be used in on grade concrete slabs such as houses, childcare centres, schools and industrial floors.
Made from 100% recycled non-toxic polypropylene, think car battery cases and bumper bars, the Cupolex domes interconnect to create a self-supporting, void forming structure. The Cupolex concrete slab system can also provide significant reductions in the volume of concrete, reinforcing steel and labour required over traditional construction methods.
Polystyrene waffle pods have been creating headlines with concerns over their potential pollution headaches and the significant volume of waste material generated in their usage. Furthermore, should the waffle pod house be demolished in the future all concrete, waffle pods and contaminated site soils will need to go directly to landfill, unlike the dome system which can be removed during demolition recycled and allow for all the associated concrete to be recycled as well.
A study by Cupolex has shown for an average house slab built within a 100km radius from the centre of Sydney they are able to provide a 492.45Kg reduction of CO2 into the atmosphere compared to this traditional slab construction method. Download this report here.
Specifying and using Cupolex as part of your concrete supply package is likely to reduce cost, enable faster and simpler construction, provide a safer working environment, reduce waste and provide a significant sustainability upside. See how the Suburban Land Agency recently engaged with this technology on their Whitlam display village precinct to showcase exciting, sustainable and environmentally responsible design.
Interested in seeing the impact Cupolex could have on sustainability and cost in your next project? Click here.
4. Maturity Testing and SmartRock Sensors
Early, rapid, and accurate in-situ estimation of the compressive strength of concrete is one of the major challenges for the concrete industry. A practical solution for such challenges can prevent millions of dollars of extra annual spending for the construction industry and asset owners. More so, with regards to concrete sustainability, we can now design a concrete for the elements early age strength not a test cylinder. How does this affect sustainability?
Maturity Testing under ASTM C1074, Standard Practice for Estimating Concrete Strength by the Maturity Method has been an international concrete testing standard since 1980. It is based on an equation that takes into account concrete temperature, time, and strength gain. We use this data as an accurate way to determine real-time strength values of curing concrete.
Under traditional test methods, we cast and crush concrete cylinders to determine the early age strength of concrete. The early age test results are used to ensure we can safely enact further construction processes such as post tensioning, loading decks, landing a fixing precast facades, stripping formwork and other time critical actions. A concrete cylinder is a very small volume of concrete with a very large surface area. When the sample cylinder is cast it immediately begins to lose heat, this heat loss is a loss of heat of hydration the chemical process concrete goes through when gaining early strength. When compared to the mass of concrete we pour in the structure the cylinder has a very slow strength gain as opposed to the element which is retaining heat in its mass and rapidly gaining strength. Therefore we are forced to over design concrete mixes to ensure the cylinder can achieve a test strength, not the element which would have achieved its required strength hours, or even days, earlier.
Want to know more about creating sustainable concrete with SmartRock and Maturity Testing? Click here.
By measuring the element for early age strength instead of the cylinder (Note: We still require 28 day cylinders under AS3600) we can now look at the opportunity to create a more sustainable concrete mix in reducing the binder content, being the cement which is contributing to the high CO2 emissions of concrete, to build a concrete mix most suited to the concrete’s real structural requirement not that of the cylinder.
Specifying and using Giatec SmartRock Sensors as part of your concrete supply package allows the ready-mix concrete supplier to provide a smarter and more sustainable mix. The cost engagement is likely cost neutral compared to traditional test methods, but there is a huge upside on construction safety, scheduling and timelines. Many projects reporting a day plus per level or pour cycle saving in their projects.
Want to know more about the role Giatec’s AI software is optimising smart and sustainable concrete mixes? Click here.
Want to discuss the impact SmartRock could be having on both your construction timeline and structures sustainably? Speak with one of our gurus today. Contact us.
5. ZeoGlass
On an international scale, in the interests of sustainability, foreign governments have begun limiting the importation of recyclable materials. Locally on January 1 2021, the Australian government enacted the Recycling and Waste Reduction Act, seeing the phased ban on the export of waste, paper, plastic, glass and tyres. This has created a shift in thinking and inspired the Australian construction industry to step it up with a number of innovative solutions hitting the marketing as we all look to play our part.
One of these innovations comes from Bluey Technologies in their ZeoGlass. Throughout their extensive R&D program Bluey were able to find a home for recycled glass in their specialist shotcrete and repair mortar of the highly corrosive sewerage environment. (Want to know more about concrete deterioration in sewerage environments? Click here). ZeoGlass is manufactured using around 60% recycled glass and waste material. When applied to existing concrete structures in a waste water environment they have found this technology increases the life of the repair in a sewerage environment from 15 years to 40 years. Not only are we able to find a practical use for glass that would otherwise be waste, we are now using it to build smarter and extend the service life of critical infrastructure.
Want to know more about ZeoGlass? Click here.
Want to know more about the deterioration of concrete in a sewerage environment? Click here.
6. Masterlife 300D
Crystalline admixtures have long played a role in the waterproofing of concrete elements. However, did you know that many of the same benefits crystalline admixtures provide concrete can also provide a huge benefit in concrete durability and sustainability?
We all know how amazing concrete is as a construction medium, but it has its vulnerabilities, especially when it comes to water. Crystalline admixture can go a long way to address these issue and dramatically improve the life of concrete.
The chemical reaction of a crystalline admixture cause additional growth of micro crystalline structures within the concrete matrix. MasterLife 300D initially increase the density of the concrete, closing off the pores and microstructure cracking in the structure which are the traditional pathways for water, and other concrete nasties such as chlorides, to get into the structure and attack the reinforcement. By closing these off we are able to greatly reduce the durability and sustainability of the concrete element. Once in the structure, MasterLife 300D technology is able to continue to react long into the future, should hairline cracking become present and water ingress occur to provide ongoing protection.
Want to know more about specifying and using MasterLife 300D in your next project? Speak with us today.
7. Upgrade with Carbon Fibre Reinforcing
Many of the bridges and structural infrastructure elements around Australia are heading towards the end of their life expectancy. Interestingly it not always concrete cancer or carbonation which sees us looking to retire and replace infrastructure. One of the situations which can lead to the removal and replacement of these assets is the purpose we need them for starts to exceed their design capability.
Carbon Fibre Reinforcing is the technology being applied across Australia to save many of these asset from a complete tear down and rebuild.
Utilising Carbon Fibre Reinforced Polymer or FRP fabric systems for strengthening and applying retrofit upgrades is considered an excellent methodology. This due to a number of factors, including its superior mechanical properties and high tensile strength and durability when compared to other options such as prefabricated PRF products. The flexibility in the application of these products allows for existing structures to be upgraded to fit their new purpose and prevents the significant wastage and consumption that would be created in the demolition and reconstruction of completely new infrastructure.
Want to know more about the use of FRP on your asset? Speak with our team today.
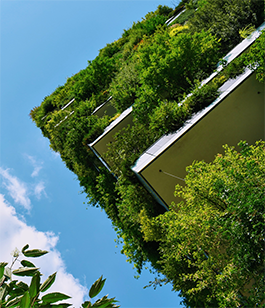